Discussion of TABC-related matters
-
Ray White
- Posts: 622
- Joined: Fri Feb 09, 2018 2:22 pm
Post
by Ray White » Mon Sep 13, 2021 2:34 am
My new body tub does not have the tacking strips needed for the wheel arch covering trim. Sherrell says these were fibreboard and held onto the body irons with split rivets BEFORE the wheel arches were fitted.
Is this a common situation. ? and how have others tackled it.? There might just be enough clearance to bend the tails of the rivets over but how secure a fitting it would make I am not sure.
Perhaps self tapping screws would be better?
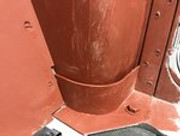
-
Ray White
- Posts: 622
- Joined: Fri Feb 09, 2018 2:22 pm
Post
by Ray White » Mon Sep 13, 2021 9:03 am
Also, the seat adjusting bracket that is revetted to the wheel arch is flat. The wheel arch is curved.
What gives??
-
bloodysalmon
- Posts: 230
- Joined: Mon Jan 22, 2018 4:10 am
- Location: Nottinghamshire, UK
Post
by bloodysalmon » Mon Sep 13, 2021 10:55 pm
Hi Ray, I can confirm that the padded area between the 'out-riggers' and the inner rear wing was indeed bridged by fibre-board. However I've used strips of sticky neoprene sponge (none-absorbent) which works nicely as a anti-rattle (metal against metal joint) material finish. However, for originality the fibreboard was fixed with split (bifurcated) rivets, and still impregnated together 75 years on ...how you do this is really up to you, especially if you can make it better.
The brackets you refer too do come flat based, which when fitted along with the covered inner wheel arch material wont be easily seen ... just a design oversight, but its right. These were flat rivetted but can be countersunk screwed.
Chris Blood - TC2686& TC3615
-
Ray White
- Posts: 622
- Joined: Fri Feb 09, 2018 2:22 pm
Post
by Ray White » Tue Sep 14, 2021 1:28 am
Thanks Chris. I think the wheel arch cover will just need to be stuck down in that corner so I am thinking of using some 1/8" double sided self adhesive rubber strips (used for furniture feet). I will also fill in the gap to stop water getting in.
My wheel arch brackets were already countersunk but the shape of the bracket will have made for poor drilling access to the hole... so that is probably why they have not been done very well... and I suspect why they were riveted in the first place.! I had them re chromed because at over £100 per pair for new ones, it was getting silly!
I have sorted four 5/16" slot head countersunk machine screws which sit flush in the bracket. With nuts and spring washers on the underside they should be fine.
-
i.thomson
- Posts: 57
- Joined: Mon Jan 07, 2013 10:16 am
Post
by i.thomson » Fri Sep 17, 2021 1:12 am
I would be very wary of using fibreboard there. What's the use of doing a rebuild, cutting out all the rust and reintroducing the very substance which creates the problem in the first place. The factory never expected our cars to last so long so was probably justified in building in this moisture trap but modern adhesives and closed cell plastics provide a better solution than was available then - and besides, they are not on show.
Ian
-
Ray White
- Posts: 622
- Joined: Fri Feb 09, 2018 2:22 pm
Post
by Ray White » Fri Sep 17, 2021 1:50 am
I think there may be some crossed wires. I am referring to the "tacking strip" for the wheel arch trim that is affixed to the curved steel part of the sub frame known as a "body iron"... not the gap between it and the wheel arch. The 3/4" x 1/8" x 6 3/4" tacking strip - according to Sherrell page 230 - is made of fibre board and is held on by two bifurcated rivets.
I am sure it would be possible to stick the trim to the wheel arch without this strip.
With regard to the gap between the wheel arch and the curved section of body iron that is open to the ground I have filled it by soaking some spongy foam rubber with PVA and pushed it down the gap. It has dried and now provides a water proof seal.
I had thought of using expanding foam but it is uncontrollable and gets everywhere.
-
cdrolshagen
- Posts: 113
- Joined: Tue Dec 29, 2015 1:30 am
- Location: Soerup Germany
Post
by cdrolshagen » Fri Sep 17, 2021 3:09 am
Hi,
hope that helps,

- IMGP1677.JPG (131.53 KiB) Viewed 2208 times

- IMGP1676.JPG (137.73 KiB) Viewed 2208 times

- IMGP1675.JPG (152.44 KiB) Viewed 2208 times
cheers Carl
-
i.thomson
- Posts: 57
- Joined: Mon Jan 07, 2013 10:16 am
Post
by i.thomson » Fri Sep 17, 2021 9:36 am
Ray. You do realise that PVA is water soluble? I wouldn't call it waterproof.
Ian.
-
Ray White
- Posts: 622
- Joined: Fri Feb 09, 2018 2:22 pm
Post
by Ray White » Fri Sep 17, 2021 10:04 am
i.thomson wrote: ↑Fri Sep 17, 2021 9:36 am
Ray. You do realise that PVA is water soluble? I wouldn't call it waterproof.
Ian.
https://www.screwfix.com/p/no-nonsense- ... 5ltr/8115p
In my case the tacking strip should have been fitted BEFORE the wheel arches (like in the photos above) but having waited TWO YEARS for my body tub to be delivered from MG Ash Frames I was not about to send it back!
Like they say...if you want a job done properly, do it yourself.